レーザー焼結 SLS
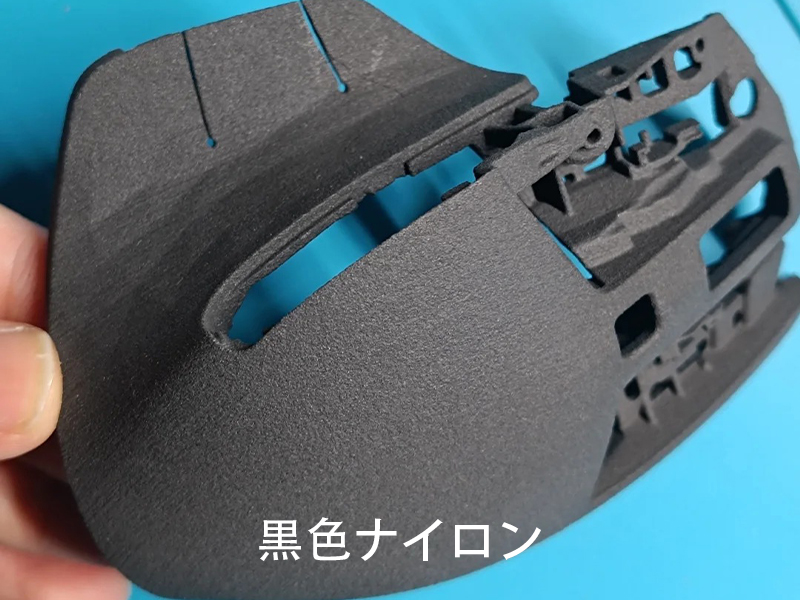
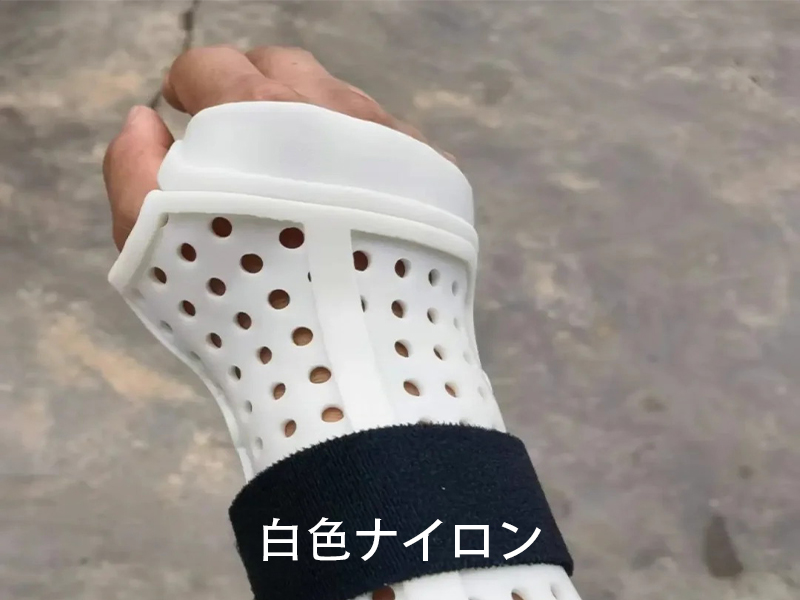
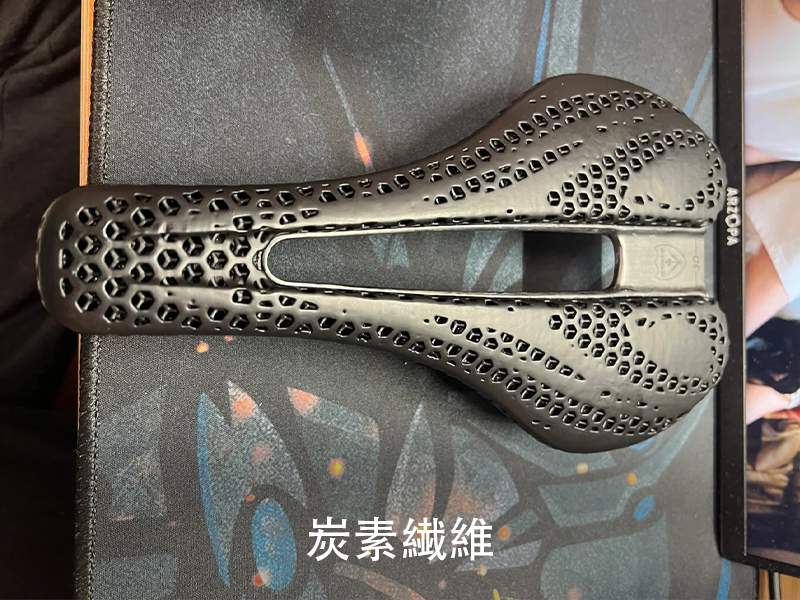
選択的レーザー焼結方式(SLS: Selective Laser Sintering) は、3Dプリンティング技術の一種で、粉末状の材料をレーザーで局所的に溶かし(焼結し)、一層ずつ積み重ねて立体物を作り上げる技術です。この技術は、プラスチック、金属、ガラス、セラミックなど多様な粉末素材に対応できるため、特に産業分野で広く利用されています。
SLSのプロセス
- 粉末材料の敷設: 造形材料(通常はナイロンなどのプラスチック粉末)を薄く均一に敷きます。
- レーザーによる焼結: レーザーが選択的に粉末に照射され、設計データに基づいて粉末を局所的に溶かし固めて層を形成します。焼結されなかった粉末はそのまま残り、次の層をサポートする役割を果たします。
- 新しい層の敷設: 焼結が終わると、次の層の粉末が敷かれ、同様にレーザーで焼結します。このプロセスを繰り返して、3Dモデルを完成させます。
- 後処理: 造形が完了した後、未焼結の粉末を取り除きますが、この粉末は再利用できることが多いです。
SLSのメリット
- サポート材が不要: SLSでは、焼結されなかった粉末が造形物を支える役割を果たすため、追加のサポート材が不要です。これにより、複雑な形状の造形が可能で、サポート材の後処理が不要になります。
- 強度と耐久性のある部品が作れる: SLSは、機械的に強度が高く、耐久性のある部品を作成できます。特にエンジニアリングプラスチックを使用することで、実用性のある部品や機械部品の製作が可能です。
- 複雑な形状の再現が可能: SLSは、細かいディテールや内部構造を持つ複雑な形状でも問題なく造形できるため、機械部品やアーティスティックなデザインにも対応可能です。
- 多様な材料の使用: SLSは、ナイロン、ポリアミド、ガラス繊維強化素材、金属粉末など、幅広い材料に対応しており、用途に応じて最適な材料を選べます。耐熱性や柔軟性のある材料も選択可能です。
- 大量生産やプロトタイピングに適している: 迅速に高精度なプロトタイプを作成でき、また粉末の再利用も可能なため、コスト効率が高く、大規模生産にも適しています。
- 最終製品としての使用が可能: 高い強度と精度を持つ部品が作れるため、試作だけでなく、最終製品の製造にも使われることが多いです。
SLSのデメリット
- 設備コストが高い: SLSプリンターは、一般的なFDM方式のプリンターに比べて高価です。また、レーザー装置や粉末材料の扱いには専用の環境が必要です。
- 表面仕上げが粗い: 造形された部品の表面はややザラついた質感になり、滑らかな仕上がりを求める場合は後処理が必要です。
- 材料の取り扱いが難しい: 特に金属粉末などは、扱いに注意が必要で、適切な設備や安全対策が求められます。
SLSは、強度や耐久性が求められる部品製造、プロトタイプ製作、そして最終製品の生産において非常に有効で、特に工業製品や自動車、航空宇宙分野などで広く利用されています。